Pioneering Biofuel Production: Transforming Biomass into Sustainable Aviation Fuel
In an effort to advance sustainable aviation, researchers from TNO and Fraunhofer UMSICHT have developed innovative methods to produce biofuel from biomass feedstocks, focusing on converting five-carbon saccharide fractions from lignocellulosic biomass into jet fuel. The aim is to demonstrate these technologies at a Technology Readiness Level (TRL) of 3-4, making them viable for future industrial applications.
The HIGFLY project employed two primary routes to produce jet fuel. The first route involved the cross-condensation of furfural and acetone, followed by mild hydrogenation and hydrodeoxygenation (HDO). The second route focused on the self-condensation of cyclopentanone (CPO) through gas phase condensation and subsequent HDO.These processes aimed to convert biomass-derived intermediates into hydrocarbons suitable for blending with jet fuel, achieving a carbon efficiency of at least 80%.
Cross-condensation of furfural and acetone
In the furfural-acetone route, researchers produced approximately 200-250 grams of fuel sample.This process began with the liquid phase condensation of furfural and acetone, which was performed in batch to scale up to sufficient amounts of the intermediate product. Multiple HDO runs were needed to achieve a transparent, stable fuel from the intermediate product.Despite challenges with catalyst deactivation, the final product contained 52% linear alkanes and had a total carbon yield of 88%.The fuel was then distilled to separate suitable fractions for further testing, achieving a carbon and hydrogen content of 96-99% and an oxygen content of 0.8-1.3%.
Self-condensation of cyclopentanone
Via the CPO route, researchers produced approximately 400 grams of fuel sample.This process utilised gas phase condensation and HDO to produce a hydrocarbon mixture primarily consisting of bi- and tri-cyclic components.The gas phase condensation was carried out at 360°C, using a selected catalyst.The feed mixture consisted of 25% mol n-octane and 75% mol cyclopentanone, with a weight hourly space velocity (WHSV) of 6 mmol g-1 h-1. The condensation process was performed in three batches over three weeks, with fresh catalyst loaded each week.
The gas phase condensation resulted in a high mass yield of 99.6% wt, indicating minimal formation of gaseous side products. The conversion rates varied between 43% and 10%, with the main product, 2-cyclopentylidene-cyclopentanone (DCPOe), yielding between 34% and 9%. The saturated condensation product, 2-cyclopentyl-cyclopentanone (DCPO), had a yield between 0.6% and 3%, while the tricyclic intermediates yielded between 0% and 10%.
The resulting intermediate products were distilled to remove n-octane, unconverted cyclopentanone, and other side products, leaving behind the high boiling bi- and tricyclic components.These components were then subjected to HDO in a fixed-bed reactor system with a selected catalyst. The HDO process was conducted in three runs at 270°C with a stoichiometric hydrogen excess of four, achieving a full HDO of the intermediates.
The HDO process resulted in a product yield of 97.6% wt in the first run, with methane formation accounting for 0.9% wt.The second run had similar results, while the third run showed a product yield exceeding 100% wt due to the addition of hydrogen. The carbon loss due to methane formation was minimal, resulting in a maximum possible carbon yield of 98.8%.
The final product mixture was distilled under vacuum to produce 16 different cuts, with the first fraction accounting for 41% of the fuel sample. The distillation process helped separate the remaining light cyclopentanol, oxygenated cC10, and other heavy oxygenated compounds. The suitable fuel cuts contained 98.9-99.8% carbon and hydrogen and 0.5-2.3% oxygen.
Further testing
The distilled fuel samples from both routes were provided to SkyNRG for further testing of relevant aviation fuel properties.These analyses are crucial for determining the suitability of the produced fuels for sustainable aviation applications.
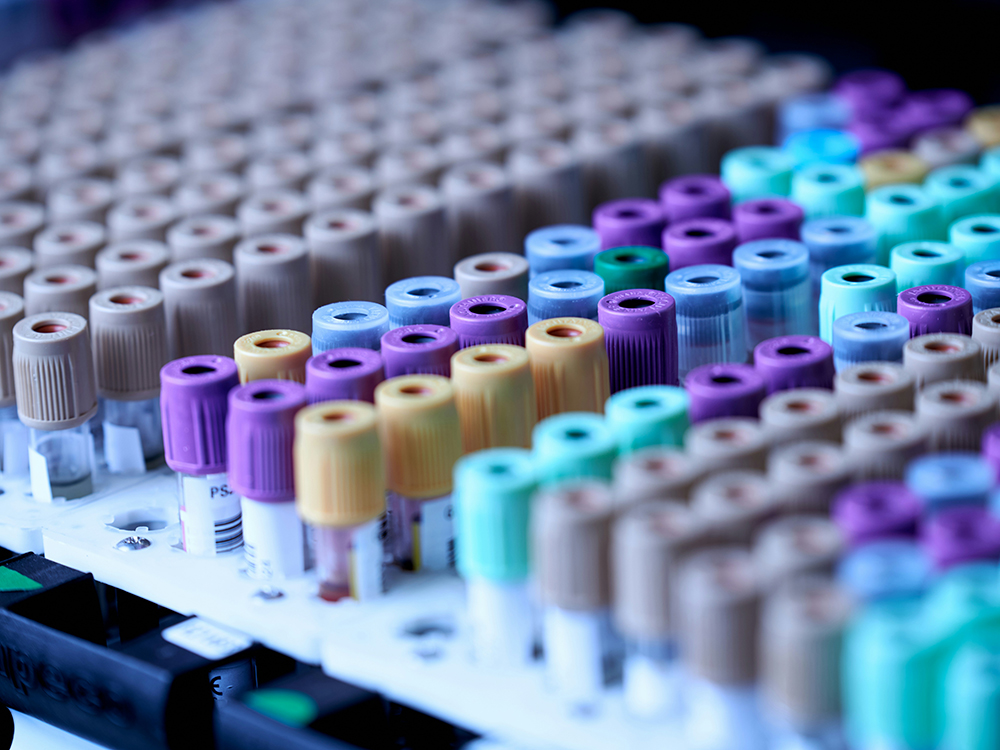
Aviation fuels must meet stringent quality standards, particularly JET A-1 and Jet A (used in the USA) for civil aviation. For HIGFLY jet fuel blends, the goal is to meet ASTM standard D7566, which outlines essential physical and chemical requirements, including flash point minimums and freeze point maximums. This testing will assess HIGFLY jet fuel properties for ASTM compliance, helping to identify the feasible blending ratios and any limitations for certification.
The potential of biomass-derived intermediates to produce biofuel
One of the critical aspects of the research was validating the use of biomass-derived furfural and bio-oxygenates in the developed processes.Tests revealed that impurities in the solvents used for furfural production led to significant catalyst deactivation, necessitating purification of furfural before the condensation process.Similarly, the high water content in CPO samples posed challenges for processing, indicating the need for concentration or purification before jet fuel production.
However, a huge amount of progress and knowledge has been gained through the research into the synthesis of jet fuel hydrocarbons from furfural and bio-oxygenates that advances our understanding of how different catalysts perform in bio-oxygenate reactions. Key findings include:
- Catalyst Performance in Batch Condensation Reactions: The study assessed the activity and selectivity of solid catalysts under batch conditions for furfural and acetone condensation, identifying catalysts that offer optimal performance.
- Continuous Flow Catalysis for Furfural and Acetone: The effectiveness of solid catalysts was further tested in continuous flow setups, revealing how continuous processing affects catalyst efficiency in furfural and acetone reactions.
- Gas-Phase Catalysis with Mixed Reactants: Activated carbon-based and solid basic catalysts were analysed under continuous gas-phase flow with cyclopentanone, furfural, and ethanol. This provided insight into how these conditions impact catalyst stability, selectivity, and activity.
- Hydrotalcite Catalyst Optimisation: The study focused on how reaction conditions, such as temperature and feed composition, influence conversion, selectivity, and lifespan of hydrotalcite catalysts during furfural condensation reactions.
- Cyclopentanone Self-Condensation: The research explored the effects of feed mixture, catalyst lifespan, and process parameters on conversion, selectivity, and reactivation potential in cyclopentanone self-condensation.
- Hydrodeoxygenation of Aldol Products: For the production of jet fuel hydrocarbons, the study examined the activity, selectivity, and properties of Ni, Pd, and Pt catalysts in the hydrodeoxygenation of furfural-acetone and related aldol products, identifying effective conditions for this process.
- Hydrogenation of Aldol Products: Testing the activity and selectivity of different catalysts in the hydrogenation of furfural-acetone-furfural aldol products in batch conditions provided insights into optimal catalyst choices.
- Hydrogen Recycling with Cyclopentanone Intermediates: The study included the hydrogenation of cyclopentanone intermediates, using hydrogen recycling techniques to enhance reaction sustainability.
- Partial Hydrogenation for Catalyst Stability: Researchers assessed the impact of mild partial hydrogenation conditions on catalyst performance, demonstrating how controlled severity can stabilise aldol products before complete hydrodeoxygenation.
- Continuous Fixed-Bed Reactor Optimisation: Using a continuous fixed-bed reactor setup with gas recycling, the study examined how process parameters affect hydrodeoxygenation of cyclic intermediates, valuable for scaling these reactions industrially.

Further research was also conducted on catalyst regeneration and performance with unpurified biomass feedstocks:
- Effect of Calcination Temperature on Hydrotalcite Catalyst: The study investigated how calcination temperature influences the properties and catalytic performance of regenerated hydrotalcite, especially in furfural and acetone condensation reactions.
- Regeneration Procedures for Alumina Catalysts: Procedures for regenerating alumina catalysts were developed and tested, evaluating their effects on conversion rates, catalytic activity, and lifespan.
- Testing Hydrotalcite Catalysts with Biomass-Derived Furfural: The activity, selectivity, and longevity of hydrotalcite catalysts were tested with unpurified, biomass-derived furfural solutions in various solvents, providing insights into real-world feedstock compatibility.
- Alumina Catalysts with Water-Containing Biomass Samples: Alumina catalysts were evaluated for their activity and selectivity with water-containing biomass-derived cyclopentanone samples, revealing their resilience and performance in moisture-rich environments.
HIGFLY´s research offers findings for optimising catalytic processes in bio-based jet fuel synthesis and the production of bio-based chemicals, offering valuable knowledge on catalyst selection, regeneration, and operational conditions. Overall, the research highlights the potential of biomass-derived intermediates in producing advanced biofuels and chemicals, paving the way for future research and development in this area.